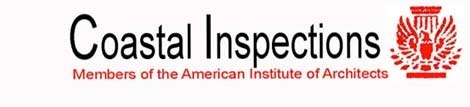
Website: http://www.Coastalinspections.org
Email: reza@coastalinspections.org
Phone: (949) 444-8033
Inspector's phone: (949) 291-7611
Monarch Beach, California
Inspector: Reza Limonadi AIA
Property Inspection Report
Client(s): |
Home Buyer |
Property address: |
1234 Perfect Street Ocean, California |
Inspection date: |
Saturday, September 22, 2012 |
This report published on Tuesday, April 29, 2014 9:39:56 AM PDT
Thank you for using Coastal Inspections for your inspection needs. I appreciate your business.
The following written report is prepared for the sole, confidential and exclusive use of the client(s) named above. It is designed to highlight major and significant defects observed on the day of the inspection, not minor or cosmetic ones (although these will be noted when observed as a courtesy). The report is intended as a general guide to help you evaluate the home. Read your entire Home Inspection Report before purchasing the property, paying close attention to all items noted on the report and to any exclusions and limitations listed. Any items noted that require further evaluation, any items not accessible or able to be located during the inspection and any items listed under the Visual Obstructions and Exclusions section should be investigated or evaluated before you purchase the home. I recommend that any needed repairs be made by a licensed, qualified contractor.
Your Home Inspection Report represents my good-faith opinions on the subjects listed within on the day of the inspection - no guarantee or warranty is either expressed or implied. Hidden or concealed defects are not included in this report. This report is not an insurance policy. Please be sure to read the entire report thoroughly and call promptly with any questions or concerns. This report shall supersede any written or verbal communication and comments made prior to providing the written report.
Best Wishes,
Reza Limonadi AIA
Registered California Architect
Licensed General Contractor
Certified Building Inspector
Certified Mold and Asbestos Inspector
Coastal Inspections
Inspector Introduction
Reza Limonadi AIA is an InterNACHI Certified Inspector for existing and new residential & commercial buildings under ASHI or CREIA & ASTM standards, Registered State of California Architect with over 20 years of experience in the construction of commercial, industrial and residential buildings, Licensed General Building Contractor (CSLB) specializing in residential constructions and renovations, Certified Residential and Commercial Mold Inspector, Certified Asbestos Building Inspector (EPA-HUD), and Indoor Air Quality inspector.
I have over 30 years cumulative experience in general building design and construction, residential and commercial property inspections, and environmental assessments and remediation (mold, asbestos, lead, radon, and indoor air quality). In addition, I am an active member of American Institute of Architects (AIA), InterNACHI, and International Association of Certified Indoor Air Consultants.
How to Read this Report
This report is organized by the property's functional areas. Within each functional area, descriptive information is listed first and is shown in bold type. Items of concern follow descriptive information.
Concerns are shown and sorted according to these types:
 | Safety | Poses a risk of injury or death |
 | Major Defect | Correction likely involves a significant expense |
 | Repair/Replace | Recommend repairing or replacing |
 | Repair/Maintain | Recommend repair and/or maintenance |
 | Future improvements | Recommended correction for future improvements |
 | Maintain | Recommend ongoing maintenance |
 | Evaluate | Recommend evaluation by a specialist |
 | Monitor | Recommend monitoring in the future |
 | Serviceable | Item or component is in serviceable condition |
 | Comment | For your information |
Click here for a glossary of building construction terms.Contact your inspector If there are terms that you do not understand, or visit the glossary of construction terms at http://www.reporthost.com/glossary.asp
General information
Inspector's name: Reza Limonadi AIA
Structures inspected: Single Family Detached
Inspection Fee: $
Payment method: Check
Present during inspection: Client(s), Realtor
Occupied: No
Weather conditions: Clear
Temperature: Warm
Ground condition: Dry
Foundation type: Crawlspace
The following items are excluded from this inspection: Security system, Irrigation system, Low voltage outdoor lighting, Fire suppression system
1) 
This structure is in an overall good condition with no deferred maintenance issues or concerns, and is in a good overall structural condition, with no signs of settlement or stress cracks visible, except as noted in this report.
 Photo 1-1
| |
2) 
Structures built prior to 1979 may contain lead-based paint and/or asbestos in various building materials such as insulation, air ducts, siding, and/or floor and ceiling tiles. Both lead and asbestos are known health hazards. Evaluating for the presence of lead and/or asbestos is not included in this inspection. The client(s) should consult with specialists as necessary, such as industrial hygienists, professional labs and/or abatement contractors for this type of evaluation. For information on lead, asbestos and other hazardous materials in homes, visit these websites:
Exterior
Foundation material: Poured in place concrete
Apparent wall structure: Wood frame
Wall covering: Stucco
Driveway material: Poured in place concrete
Sidewalk material: Poured in place concrete
Exterior door material: Solid core wood
3) 


One or more trip hazards were found in the driveway due to cracks, settlement and/or heaving. Recommend having a qualified contractor evaluate and repair or replace driveway sections as necessary to eliminate trip hazards.
 Photo 3-1
|
 Photo 3-2
|
 Photo 3-3
| |
4) 

One or more hornet, bee and/or wasp nests were found. These can pose a safety hazard. Nest(s) should be removed as necessary.
 Photo 4-1
| |
5) 

The driveway has significant cracks and/or deterioration in one or more areas. A qualified contractor should evaluate and repair or replace driveway sections as necessary.
 Photo 5-1
|
 Photo 5-2
|
6) 
One or more gutters are missing. This can result in water accumulating around the structure's foundation, or in basements and crawl spaces if they exist. Accumulated water is a conducive condition to wood destroying insects and organisms, and may also cause the foundation to settle and possibly fail over time. Install gutters and downspouts where missing. Also, extensions such as splashblocks or tie-ins to underground drain lines should be installed as necessary to carry rain water away from the house.
 Photo 6-1
|
 Photo 6-2
|
7) 
Vegetation such as trees, shrubs and/or vines are in contact with or less than one foot from the structure's exterior. Vegetation can serve as a conduit for wood destroying insects and may retain moisture against the exterior after it rains. Vegetation should be pruned and/or removed as necessary to maintain a one foot clearance between it and the structure's exterior.
 Photo 7-1
| |
8) 
Other concerns.
9) 
This structure's exterior components is in a good overall condition with no major maintenance concerns, except as noted in this report.
 Photo 9-1
|
 Photo 9-2
|
 Photo 9-3
| |
10) 
Minor cracks were found in sidewalk or patio sections. However they don't appear to be a structural concern and no trip hazards were found. No immediate action is recommended, but the client(s) may wish to have repairs made or have cracked sections replaced for aesthetic reasons.
 Photo 10-1
|
 Photo 10-2
|
Roof
Roof inspection method: Traversed
Roof type: Hipped
Roof covering: Asphalt or fiberglass composition shingles
Gutter & downspout material: None
Roof ventilation: Adequate
11) 
Trees are overhanging roof and are within 10 feet of roof vertically. This is a conducive condition for wood destroying insects and organisms since organic debris such as leaves or needles are more likely to accumulate on the roof surface. Accumulated debris may cause water to enter gaps in the roof surface and leak into attic and/or interior spaces. Trees should be pruned so they are at least 10 feet above roof, or don't overhang the roof.
 Photo 11-1
| |
12) 
Composition tabbed shingles are installed on roof sections with a slope less than 3/12 (three inches rise for every 12 inches run). Most shingle manufacturers won't warranty composition shingles if used on a roof with a slope less than 3/12. Monitor the roof and interior spaces below for leaks in the future. Ideally, or if leaks occur, a qualified roofing contractor should replace the roof surface with materials intended for low slopes such as a "torch down" roof.
 Photo 12-1
| |
13) 
Roof is in serviceable condition showing no signs of extensive wear or deferred maintenance, except as noted in this report.
 Photo 13-1
|
 Photo 13-2
|
 Photo 13-3
|
 Photo 13-4
|
 Photo 13-5
|
 Photo 13-6
|
Garage
14) 

There are large slab cracks in the garage floor slab. Garage slab is not a part of the structural slab in this structure, and the cracks does not indicate a major structural concern. Replace the garage's concrete slab with a new slab, metal reinforcement, and moisture barrier.
 Photo 14-1
|
 Photo 14-2
|
15) 
Cover plate(s) are missing from one or more electric boxes, such as for receptacles, switches and/or junction boxes. They are intended to contain fire and prevent electric shock from exposed wires. This is a safety hazard due to the risk of fire and shock. Cover plates should be installed where missing.
 Photo 15-1
|
 Photo 15-2
|
16) 
Other concerns.
 Photo 16-1
Missing roof sheathing board
|
 Photo 16-2
Moisture stains on sill plate
|
17) 
Garage vehicle door is in a good condition displaying no signs of stress and or excessive wear. This garage door has all needed components such as sides and bottom weather stripping, and functioned correctly at the time of inspection.
 Photo 17-1
|
 Photo 17-2
|
18) 
This garage is in a good overall condition with all components functioning correctly, except as noted in this report.
 Photo 18-1
|
 Photo 18-2
|
19) 
There is no automatic garage door opener installed in this garage.
 Photo 19-1
| |
Attic
Inspection method: Viewed from hatch
Roof structure type: Rafters
Ceiling structure: Ceiling beams
Insulation material: Fiberglass loose fill
20) 


Evidence of "light to moderate" rodent infestation was found in one or more areas. The Center for Disease Control (CDC) defines this as less than 20 feces per square foot. Rodent infestation may be a safety hazard due to the risk of contracting
Hantavirus Pulmonary Syndrome (HPS). HPS is a rare (only 20-50 cases per year in the United states) but deadly (40% mortality rate) disease transmitted by infected rodents through urine, droppings, or saliva. Humans can contract the disease when they breathe in aerosolized virus. For example, from sweeping up rodent droppings.
Recommend following guidelines in the CDC's
Clean Up, Trap Up, Seal Up article for eradicating rodents, cleaning up their waste and nesting materials, and preventing future infestations. While Hantavirus is believed to survive less than one week in droppings and urine, specific precautions should be taken during clean up. The client(s) may wish to consult with a qualified, licensed pest control operator for eliminating the infestation. A qualified licensed abatement contractor or industrial hygienist could be contacted for clean up. If the infestation was minimal, clean up of rodent waste and nesting materials in non-living spaces (crawl spaces and attics) may not be necessary, or may be performed for aesthetic reasons only (odor and appearance).
 Photo 20-1
|
 Photo 20-2
|
21) 

Ventilation is substandard in the attic. Inadequate attic ventilation may result in high attic and roof surface temperatures, reduce the life of the roof covering materials and increase cooling costs. High levels of moisture are also likely, and can be a conducive condition for wood destroying insects and organisms. Standard building practices require one square foot of vent area for 150 to 200 square feet of attic space. Vents should be evenly distributed between soffits, ridges and at corners to promote air circulation. A qualified contractor should evaluate and install vents as per standard building practices.
 Photo 21-1
|
 Photo 21-2
|
22) 
The ceiling insulation's R rating is significantly less than what's recommended for this area. Recommend having a qualified contractor install additional insulation as per standard building practices for better energy efficiency.
23) 
No insulation is installed over the attic access hatch. Recommend installing insulation above hatch for better energy efficiency.
 Photo 23-1
| |
24) 
Attic is in a good overall condition that displays adequate ventilation, proper insulation and adequate protection of all components routed through. It also displays a structural condition that is proper, secure and safe. There are no signs of excessive movement, lack of support or improper modifications to the structural components of this building.
 Photo 24-1
|
 Photo 24-2
|
 Photo 24-3
|
 Photo 24-4
|
25) 
The attic area was viewed from the access hatch. Areas beyond the inspectors visual range in the attic space are not covered in this report. Intent of this inspection is to get a sense of the house's structural make-up and stability. This inspection is not a complete attic inspection and in the case that a complete visual inspection is necessary, your inspector will inform you.
Electric service
Primary service type: Overhead
Primary service overload protection type: Circuit breakers
Service amperage (amps): 100
Service voltage (volts): 120/240
Location of main service switch: Side Yard
Location of main disconnect: Breaker at top of main service panel
Service entrance conductor material: Copper
Main disconnect rating (amps): 100
Solid strand aluminum branch circuit wiring present: No
26) 


There are no arc fault circuit interrupter (AFCI) breakers in the main service panel serving the bedrooms. This is a safety hazard due to the risk of shock and fire. A qualified electrician should evaluate and make repairs and/or replace circuit breakers as necessary.
 Photo 26-1
| |
27) 

The electrical panel box in this structure is in serviceable condition, but the panel is rated substantially less than 200 amps, and may be inadequate for the client(s) needs. Evaluate as needed and upgrade to a 200 amp service if possible.
 Photo 27-1
|
 Photo 27-2
|
 Photo 27-3
|
 Photo 27-4
|
 Photo 27-5
|
 Photo 27-6
|
28) 
Other concerns.
 Photo 28-1
This box's cover could not be opened to visually inspect this unit
| |
Water heater
Estimated age: 2008
Type: Tank
Energy source: Natural gas
Capacity (in gallons): 38
29) 

No drain line is installed for the temperature-pressure relief valve. This is a potential safety hazard due to the risk of scalding if someone is standing next to the water heater when the valve opens. A qualified plumber should install a drain line as per standard building practices. For example, extending to 6 inches from the floor, or routed so as to drain outside.
 Photo 29-1
| |
30) 
Dissimilar metal connector should be replaced with similar connections to avoid corrosion.
 Photo 30-1
| |
31) 
Water heater is in a good physical condition, displaying all needed elements such as appropriate sceismic straps, and drain lines for it's pressure relieve valve, but it did not produce hot water when inspected.
32) 
Other concerns.
Heating and cooling
Primary heating system energy source: Natural gas
Primary heat system type: Forced air
Primary A/C energy source: Electric
Primary Air conditioning type: Split system
Distribution system: Flexible ducts
Filter location: In return air duct below furnace
Note: Our inspection of major systems is limited to the normal operating functions of items listed. Independent evaluations including the adequacy/inadequacy of heating and cooling systems (such as cracked heat exchangers, air conditioning pressure tests, etc.) water flow (such as gallons per minute), electrical amperage/voltage adequacies are not within the scope of this report. If such detailed information is required, we suggest contacting appropriate specialists.
33) 
No filter is visible for the heating/cooling system. As a result, unfiltered air will flow through the system, and the heating/cooling equipment life and the indoor air quality may be reduced. Correctly sized filter(s) should be installed. If necessary, guides or retaining devices should be installed or repaired so filter(s) are securely anchored and gaps around edges are minimized.
 Photo 33-1
| |
34) 
The outside condensing unit is not securely connected to a base or to the concrete decking beneath. Damage may occur if the unit shifts due to vibration. Evaluate and repair as necessary so the unit is secure to its base.
 Photo 34-1
| |
35) 

Furnace is in serviceable condition, providing heat to the living areas when it's controls were operated, but the unit did not reach 100 f in heating mode. Service as needed.
 Photo 35-1
| |
36) 
Condenser unit is equipped with an adequate electrical shut off switch.
 Photo 36-1
| |
37) 
Condensing unit is in serviceable condition, providing needed thermal exchange to supply the living areas with cool air, when it's controls were operated.
 Photo 37-1
| |
38)
Temperatures
 Photo 38-1
Heater did not reach 100 f in heating mode. Evaluate and service as required
|
 Photo 38-2
A/C reached a minimum of 15 f below ambient temperature in cooling mode
|
 Photo 38-3
90 f ambient temperature
| |
Plumbing and laundry
Water pressure (psi): 105 psi
Location of main water meter: Sidewalk
Location of main fuel shut-off: Side yard
Water service: Public
Service pipe material: Copper, Galvanized steel
Supply pipe material: Copper, Galvanized steel
Vent pipe material: Plastic, Galvanized steel
Drain pipe material: Plastic, Galvanized steel
Waste pipe material: Plastic, Galvanized steel
39) 

The water supply pressure is greater than 80 psi. Pressures above 80 psi may void warranties for some appliances such as water heaters or washing machines. Flexible supply lines to washing machines are more likely to burst with higher pressures. Typically the pressure cannot be regulated at the water meter. Recommend having a qualified plumber evaluate and make modifications to reduce the pressure below 80 psi. Installing a pressure reducing valve on the main service pipe is a common solution to this problem. If one exists, then it should be adjusted for lower pressures.
 Photo 39-1
| |
40) 

There is no water pressure regulator installed on the main water line entering this structure. City water pressure fluctuation can cause damage to the structure's plumbing lines. It is recommended to install a pressure regulator to maintain a constant safe pressure inside the structure's plumbing lines.
 Photo 40-1
| |
41) 

Water hammering was noticed when the faucet by the garage was operated. Evaluate and repair as necessary such as installing a water hammer arrestor.
 Photo 41-1
| |
42) 
Other concerns.
 Photo 42-1
Laundry area is using a GFI outlet. Remove and exchange with a regular outlet as needed to avoid accidental tripping
| |
43) 
The main shut off valve is buried in the front planter. Remove dirt from around this valve for accessibility and ease of operation.
 Photo 43-1
| |
44) 
This laundry area is in an overall good condition with no signs of deferred maintenance, and its components in a functioning state, except as noted in this report.
 Photo 44-1
| |
45) 
This Laundry room supports a gas only dryer. The client should be advised that an electric dryer unit will not work in this laundry room layout without an electrical modification.
 Photo 45-1
| |
Crawl space
Inspection method: Viewed from hatch
Insulation material underneath floor above: None visible
Pier or support post material: Wood
Beam material: Solid wood
Floor structure above: Solid wood joists
Vapor barrier present: No
46) 

No insulation is installed under the floor in the crawl space. Recommend that a qualified contractor install R19 or better (6" thick fiberglass batt) insulation under the floor for better energy efficiency.
 Photo 46-1
| |
47) 

Wooden support posts are not securely fastened to beams above. This is a safety hazard since they can separate during a seismic event. A qualified contractor should evaluate and make repairs as necessary, such as installing metal ties, bracing with lumber and/or plywood gussets as per standard building practices.
 Photo 47-1
| |
48) 
No vapor barrier is installed. This is a conducive condition for wood destroying insects and organisms due to the likelihood of water evaporating into the structure from the soil. A qualified contractor should install a vapor barrier. Standard building practices require the following:
- The soil below the vapor barrier should be smooth and free from sharp objects.
- Seams should overlap a minimum of 12 inches.
- The vapor barrier should lap up onto the foundation side walls.
Better building practices require that:
- Seams and protrusions should be sealed with a pressure sensitive tape.
- The vapor barrier should be caulked and attached tightly to the foundation side walls. For example, with furring strips and masonry nails.
 Photo 48-1
| |
49) 
Clean and remove abandoned wiring from the crawlspace.
 Photo 49-1
|
 Photo 49-2
|
50) 
Crawlspace is in a good overal condition with all needed components in place. All ventilation ports are covered with metal mesh, with an intact access door, and a clean condition with no evidence of infestation. Crawl space conditions is good with exception of items noted in this report.
 Photo 50-1
|
 Photo 50-2
|
51)
Crawlspace was viewed from the access hatch. Areas beyond the inspectors visual range in the crawlspace are not covered in this report. Intent of this inspection is to get a sense of the house's structural make-up and stability. This inspection is not a complete crawlspace inspection and in the case that a complete visual inspection is necessary, your inspector will inform you.
 Photo 51-1
| |
Kitchen
Note: Inspection of kitchen components is limited to built-in gas or electric appliances and plumbing systems, if power is supplied. These items are tested under normal operating conditions. Extensive evaluations, such as calibration of timers, heat settings and temperature probes on cooking appliances are not within the scope of this report. Note: Due to the inaccessibility of the dishwasher components, we can do no more than operate under normal operating procedures. Dishwashers can fail at any time due to their complexity. Our review is to determine if the system is free of leaks and excessive corrosion. Shutoff valves and angle stops under kitchen or bathroom sinks and toilets are not turned or tested during the inspection due to the possibility of leaking. We suggest all shutoff valves or angle stops be turned regularly to ensure free movement in case of emergency.
52) 


One or more open ground, three-pronged grounding type receptacles were found. This is a safety hazard due to the risk of shock. A qualified electrician should evaluate and make repairs as necessary.
Grounding type receptacles were first required in residential structures during the 1960s. Based on the age of this structure and/or the absence of 2-pronged receptacles, repairs should be made by correcting wiring circuits as necessary so all receptacles are grounded as per standard building practices. Replacement of three-pronged receptacles with 2-pronged receptacles is not an acceptable solution.
 Photo 52-1
|
 Photo 52-2
|
53) 


One or more electric receptacles and/or the boxes they are installed in are loose and/or not securely anchored. Wire conductors may be damaged due to repeated movement and/or tension on wires, or insulation may be damaged. This is a safety hazard due to the risk of shock and fire. A qualified electrician should evaluate and repair as necessary.
 Photo 53-1
| |
54) 


One or more ground fault circuit interrupter (GFCI) electric receptacles did not trip when tested with the inspector's test instrument. These devices should trip when tested with a test instrument in addition to tripping via the test buttons on the receptacles. This is a safety hazard due to the risk of shock. A qualified electrician should evaluate and repair as necessary.
 Photo 54-1
| |
55) 

The range can tip forward, and no anti-tip bracket appears to be installed. This is a safety hazard since the range may tip forward when weight is applied to the open door, such as when a small child climbs on it, or if heavy objects are dropped on it. Anti-tip brackets have been sold with all free standing ranges since 1985. An anti-tip bracket should be installed to eliminate this safety hazard. For more information, visit:
http://www.google.com/search?q=range+anti+tip+device
 Photo 55-1
| |
56) 
Hood exhaust ducts are connected without use of a mechanical fasteners such as metal screws. Screw exhaust duct pieces together with metal screws or other mechanical fasteners and seal with duct tape to prevent movement and disconnection.
 Photo 56-1
| |
57) 
Handles and/or drawer pulls are not installed on one or more cabinets, where the drawers and/or doors are difficult to open without them. Recommend installing handles and/or pulls as necessary.
 Photo 57-1
| |
58) 

Hot water was shut off to the kitchen faucet. Evaluate and repair as necessary.
 Photo 58-1
| |
59) 
Gas connection to the oven is shut off. The oven did not get evaluated in this inspection.
 Photo 59-1
|
 Photo 59-2
|
60) 
Other concerns.
 Photo 60-1
Ice / water dispenser did not get evaluated
| |
61) 
This kitchen is in an excellent condition, displaying all equipments and components at their best state. There are no differed maintenance issues or other concerns in this kitchen, except as noted in this report.
 Photo 61-1
| |
Bathrooms
62) 


One or more open ground, three-pronged grounding type receptacles were found. This is a safety hazard due to the risk of shock. A qualified electrician should evaluate and make repairs as necessary.
Grounding type receptacles were first required in residential structures during the 1960s. Based on the age of this structure and/or the absence of 2-pronged receptacles, repairs should be made by correcting wiring circuits as necessary so all receptacles are grounded as per standard building practices. Replacement of three-pronged receptacles with 2-pronged receptacles is not an acceptable solution.
 Photo 62-1
| |
63) 

One or more toilets are loose or is not firmly attached to the ground. Remove the toilet(s) for further evaluation and repairs if necessary. A new wax ring should be installed and toilet(s) should be securely anchored and fully adhered to the floor to prevent movement and leaking.
 Photo 63-1
| |
64) 
One or more sink drains use flexible drain pipe. This type of drain pipe is more likely to clog than smooth wall pipe. Recommend having a qualified plumber replace this pipe with standard plumbing components (smooth wall pipe) to prevent clogged drains.
 Photo 64-1
| |
65) 
One or more sink stopper mechanisms are missing, or need adjustment or repair. Stopper mechanisms should be installed where missing and/or repairs should be made so sink stoppers open and close easily.
 Photo 65-1
| |
66) 
Seal around all penetrations into the wall system.
 Photo 66-1
|
 Photo 66-2
|
67) 
Bathrooms in this buildings are all in a good overall condition displaying proper plumbing connections, adequate ventilation, and necessary electrical components such as GFI outlets close to the sink. There are no signs of deferred maintenance, excessive moisture, or other related issues of concern, except as noted in this report.
 Photo 67-1
|
 Photo 67-2
|
68)
One or more bathroom sink drains has an active leak. For example, at pipe fittings and/or junctions between pipe and sink. A qualified plumber should evaluate and repair as necessary.
 Photo 68-1
|
 Photo 68-2
|
Interior rooms
69) 


One or more open ground, three-pronged grounding type receptacles were found. This is a safety hazard due to the risk of shock. A qualified electrician should evaluate and make repairs as necessary.
Grounding type receptacles were first required in residential structures during the 1960s. Based on the age of this structure and/or the absence of 2-pronged receptacles, repairs should be made by correcting wiring circuits as necessary so all receptacles are grounded as per standard building practices. Replacement of three-pronged receptacles with 2-pronged receptacles is not an acceptable solution.
 Photo 69-1
|
 Photo 69-2
|
 Photo 69-3
|
 Photo 69-4
|
 Photo 69-5
|
 Photo 69-6
|
70) 


Few electric receptacles and two-pronged receptacles rather than three-pronged, grounded receptacles are installed in one or more interior rooms. This can result in "octopus" wiring with extension cords. Two-prong receptacles are considered unsafe by today's standards, and limit the ability to use appliances that require a ground in these rooms. This is a safety hazard for both fire and shock. Examples of appliances that require grounded receptacles include:
- Computer hardware
- Refrigerators
- Freezers
- Air conditioners
- Clothes washers
- Clothes dryers
- Dishwashers
- Kitchen food waste disposers
- Information technology equipment
- Sump pumps
- Electrical aquarium equipment
- Hand-held motor-operated tools
- Stationary and fixed motor-operated tools
- Light industrial motor-operated tools
- Hedge clippers
- Lawn mowers
This list is not exhaustive. A qualified electrician should evaluate and install additional receptacles and grounded receptacles as per the client(s)' needs and standard building practices.
 Photo 70-1
|
 Photo 70-2
|
71) 

An insufficient number of smoke alarms are installed. Additional smoke alarms should be installed as necessary so a functioning one exists in each hallway leading to bedrooms, and in each bedroom. For more information, visit
http://www.cpsc.gov/cpscpub/pubs/5077.html
 Photo 71-1
| |
72) 

Carbon Monoxide detectors is required in all houses (1 – 4 units) if they have any of the following:
- Any gas appliances such as a gas stove, gas furnace, gas fireplace, gas water heater, etc.
- A fireplace (even if it only burns wood, pellets, or any other material).
- An attached garage (even if there are no gas appliances in the house!). Cars continue to emit CO even after they are shut off.
- ANY rental dwelling that meets the criteria listed above.
As of January 1, 2013, ALL multi-family dwellings including multi-family dwellings that meet the criteria listed above will be required to have Carbon Monoxide detectors.
The International Association of Fire Chiefs recommend a carbon monoxide detector on every floor of your home, including the basement. A detector should be located within 10 feet of each bedroom door and there should be one near or over any attached garage. Each detector should be replaced every five to six years.
Proper placement of a carbon monoxide (CO) detector is important. If you are installing only one carbon monoxide detector, the Consumer Product Safety Commission (CPSC) recommends it be located near the sleeping area, where it can wake you if you are asleep. Additional detectors on every level and in every bedroom of a home provides extra protection against carbon monoxide poisoning.
Homeowners should remember not to install carbon monoxide detectors directly above or beside fuel-burning appliances, as appliances may emit a small amount of carbon monoxide upon start-up. A detector should not be placed within fifteen feet of heating or cooking appliances or in or near very humid areas such as bathrooms.
73) 

There is one or more older style single Pane window(s) and or doors in this structure. These doors and windows are not as energy efficient or operate as smooth as the newer styles. Evaluate and replace as needed.
 Photo 73-1
|
 Photo 73-2
|
74) 

Screen(s) in one or more windows are missing. The client(s) should ask the property owner(s) about this. Screens are often removed for window cleaning and they may be stored somewhere. If not, then recommend installing screens where missing.
 Photo 74-1
| |
75) 
One or more doors will not latch when closed. Repairs should be made such as aligning strike plates with latch bolts and/or replacing locksets to have doors latch properly when closed.
 Photo 75-1
| |
76) 
Other concerns.
 Photo 76-1
Missing one pocket door pull
|
 Photo 76-2
|
77) 
Interior spaces in this building are in an overall good condition with no signs of deferred maintenance or other areas of concern, except as noted in this report.
 Photo 77-1
| |
This inspection meets or exceeds the Standards of Practice for the InterNational Association of Certified Home Inspectors (NACHI). It is intended as a general guide to help you make an evaluation as to the overall condition of the home. It is not intended to place a value on the home nor make any representation as to the advisability of purchase. It is not a guarantee or warranty. It is not an insurance policy.
The report reflects the opinion of the inspector(s), based upon visual impressions of conditions that existed at the time of inspection. The inspection is not intended to be technically exhaustive or to imply that every component in the home was inspected. No disassembly of equipment, opening of walls, moving of furniture or stored items was performed or is allowed by state requirements. All components which were concealed or obscured from observation at the time of inspection (including those concealed by clutter and stored items) are necessarily excluded from the report. Unless noted otherwise the house exterior was inspected from the ground. Only a representative sampling of parts and components (windows, electrical outlets, roof shingles, exterior wall trim and cladding, etc.) were examined and are within the scope of this inspection. Unless noted otherwise roofs and roofing materials are inspected from the ground with binoculars, from the roof edge when possible or from windows overlooking the roof.
Environmental hazards are not within the scope of the inspection and are excluded from the report. Any hazards noticed while performing the building inspection will be listed in the "Possible Environmental Hazards" section for your convenience so you can have them further investigated by an expert. These hazards include but are not limited to radon gas, carbon monoxide, lead and lead paint, buried storage tanks, asbestos, vermiculite, urea formaldehyde, and mold. Also excluded from the report are heating system heat exchangers, pools, hot tubs, spas, fountains, exterior lighting, water wells, zoning ordinances, intercoms, playground equipment, sports courts, elevators, outbuildings, septic tanks and sewage systems, water treatment equipment, security systems, sprinkler systems (both fire and lawn), bridges (over culverts, streams, ponds, etc.), generators, greenhouses, and central vacuum systems. Condo common areas are excluded. This is not an inspection for insects (including wood destroying), rodents birds, or other infestations. Reinspections or additional testing is not included and will incur an additional fee if needed. No warranty or guaranty of the home or components is implied by Coastal Home Inspections.
This inspection report is not a compliance inspection for any government codes or regulations, nor as a property or land survey. The types of water supply (public supply or private well) and waste disposal (public sewer or private septic system) cannot be accurately determined by a home inspection and were not part of your home examination. I recommend you check with your local City or other source of building records / permits to verify your type of system before purchase.