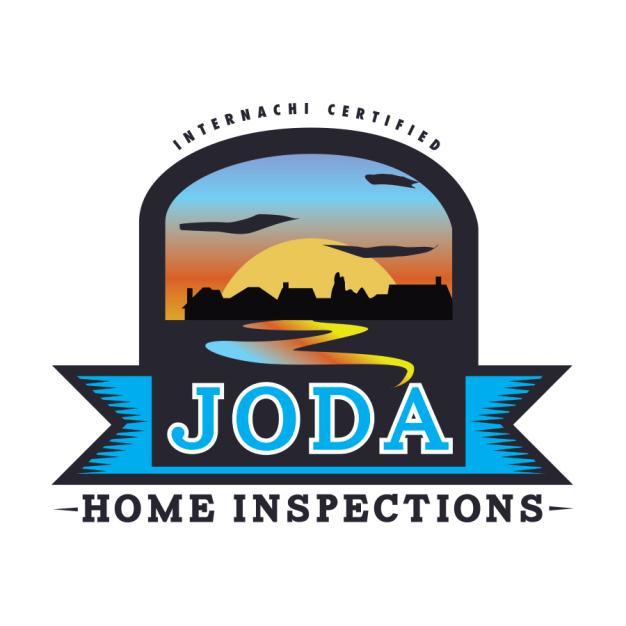
JODA Home Inspections
Website: http://JODAhomeinspections.com
Inspector's email: jodainspections@gmail.com
Inspector's phone: (801) 577-1945
Inspector: Andrew Jolley
Summary
Client(s): |
Sample |
Property address: |
123 Anywhere St |
Inspection date: |
Tuesday, May 23, 2017 |
This report published on Tuesday, May 23, 2017 11:13:08 PM MDT
This report is the exclusive property of this inspection company and the client(s) listed in the report title. Use of this report by any unauthorized persons is prohibited.
General Information
1

- Structures built prior to the mid 1980s may contain lead and/or asbestos. Lead is commonly found in paint and in some plumbing components. The EPA does not recognize newer coats of paint as encapsulating older coats of lead-based paint. Asbestos is commonly found in various building materials such as insulation, siding, and/or floor and ceiling tiles. Laws were passed in 1978 to prohibit usage of lead and asbestos, but stocks of materials containing these substances remained in use for a number of years thereafter. Both lead and asbestos are known health hazards. Evaluating for the presence of lead and/or asbestos is beyond the scope of this inspection. Any mention of these materials in this report is made as a courtesy only, and meant to refer the client to a specialist. Consult with specialists as necessary, such as industrial hygienists, professional labs and/or abatement specialists for this type of evaluation. For information on lead, asbestos and other hazardous materials in homes, visit:
http://www.reporthost.com/?EPAhttp://www.reporthost.com/?CPSChttp://www.reporthost.com/?CDC
3

- Microbial growths were found at one or more locations in interior rooms and/or bathrooms. It is beyond the scope of this inspection to identify what substance or organism this staining is. However such staining is normally caused by excessively moist conditions, which in turn can be caused by plumbing or building envelope leaks and/or substandard ventilation. These conducive conditions should be corrected before making any attempts to remove or correct the staining. Normally affected materials such as drywall are removed, enclosed affected spaces are allowed to dry thoroughly, a mildewcide may be applied, and only then is drywall reinstalled. For evaluation and possible mitigation, consult with a qualified industrial hygienist or mold/moisture mitigation specialist. For more information, visit:
http://www.reporthost.com/?MOLDCDChttp://www.reporthost.com/?MOLDEPABoth bathrooms and corner bedroom. Basement joist also had staining that could be organic.
Grounds
4

- Guardrails at one or more locations with drop-offs higher than 30 inches were missing. This poses a fall hazard. Guardrails should be installed where walking surfaces are more than 30 inches above the surrounding grade or surfaces below. Recommend that a qualified contractor install guardrails where missing and per standard building practices.
5

- I recommend that at least one more bollard be added to protect the gas meters from physical damage.
6

- Cracks, holes, settlement, heaving and/or deterioration resulting in trip hazards were found in the sidewalks or patios. For safety reasons, recommend that a qualified contractor repair as necessary to eliminate trip hazards.
Exterior and Foundation
8

- I recommend removal of the dryer vent cover screen to prevent a fire hazard.
9
- Some sections of siding and/or trim were damaged and/or substandard. Recommend that a qualified person repair, replace or install siding or trim as necessary.
Particle board type wood was found under the siding however the fiberboard was very soft and appeared to be holding water. This is conducive to rot and fungal growth.
10
- Damaged and missing fascia wrap should be repaired to prevent moisture intrusion and to protect the fascia board.
11

- Moderate cracks (1/8 inch - 3/4 inch) and/or leaning were found in the foundation. This may be a structural concern or an indication that settlement is ongoing. The client should consider hiring qualified contractors and/or engineers as necessary for further evaluation. Such contractors may include:
- Foundation repair contractors who may prescribe repairs, and will give cost estimates for such repairs
- Masonry contractors who repair and/or replace brick veneer
- Geotechnical engineers who attempt to determine if settlement is ongoing, and the cause of the settlement
- Structural engineers who determine if repairs are necessary, and prescribe those repairs
At a minimum, recommend sealing cracks to prevent water infiltration. Numerous products exist to seal such cracks including hydraulic cement, resilient caulks and epoxy sealants.
12
- Loose wires should be secured next to unit B front door.
13
- Soil was in contact with or less than 6 inches from siding, trim or structural wood. This is a conducive condition for wood-destroying organisms. Recommend grading or removing soil as necessary to maintain a 6-inch clearance. If not possible, then recommend replacing untreated wood with pressure-treated wood. Installation of borate-based products such as Impel rods can also reduce the likelihood of rot or infestation if soil cannot be removed. Note that damage from fungal rot and/or insects may be found when soil is removed, and repairs may be necessary.
Wood should be protected and painted to prevent damage from moisture and insects.
Crawl Space
14
- Ventilation for the crawl space was substandard. There were no vents visible. This can result in high levels of moisture in the crawl space and is a conducive condition for wood-destroying organisms. One square foot of vent area should be installed for 150 square feet of crawl space. Vents should be evenly distributed and within a few feet of corners to promote air circulation. Recommend that a qualified contractor install or improve venting per standard building practices.
15
- No insulation was installed under the floor above the crawl space. Recommend that a qualified person install insulation for better energy efficiency and per standard building practices. Typically this is R-19 rated fiberglass batt with the attached facing installed against the warm (floor) side.
16
- No vapor barrier was installed in the crawl space. This is a conducive condition for wood-destroying organisms due to the likelihood of water evaporating from the soil below up into the structure. A 6 mil black plastic sheet should be placed over all exposed soil with seams overlapped to 24 inches, and not in contact with any wood structural components. The sheeting should be held in place with bricks or stones, not wood. Recommend that a qualified contractor install a vapor barrier per standard building practices.
Basement
19

- Exposed paper insulation backing was visible in the basement. This is a fire hazard. I recommend that the insulation be replaced or covered. Any missing insulation should be replaced.
20

- The only entrance/exit to the basement appeared to be the basement stairs. While this is common in older homes, modern standards require a secondary escape for use in the event of fire or an emergency. Such entrances/exits should allow entry by emergency personnel and their equipment. It is beyond the scope of this inspection to verify compliance with the current codes, and codes are generally not retroactive. Consult with a window/door contractor and/or the local municipal building officials regarding egress guidelines.
This is not as large of a concern since there are no bedrooms in the basement.
21

- One or more support posts appear to have been added since the original construction based on the inspector's observations. Such posts may have been added to reduce bounce or sag in floors above. Consult with the property owner about this, or that a qualified contractor evaluate and make permanent repairs per standard building practices if necessary.
Roof
22

- The roof surface appeared to be near the end of its service life and will likely need replacing in the near future even if repairs are made now. Recommend discussing replacement options with a qualified contractor, and budgeting for a replacement roof surface in the near future. The client may also wish to consider having a qualified contractor attempt to issue a "5 year roof certificate."
24
- Many composition shingles were missing and/or damaged. Leaks can occur as a result. This is a conducive condition for wood-destroying organisms. Recommend that a qualified contractor repair as necessary. For example, by replacing shingles.
25
- Extensions such as splash blocks or drain pipes for one or more downspouts were missing. Water can accumulate around the building foundation or inside crawl spaces or basements as a result. Recommend that a qualified person install, replace or repair extensions as necessary so rainwater drains away from the structure.
26
- One or more gutters were incomplete and/or damaged. Rainwater can come in contact with the building exterior or accumulate around the building foundation as a result. This is a conducive condition for wood-destroying organisms. Recommend that a qualified person repair as necessary.
I recommend that gutters be added around the entire perimeter.
Attic and Roof Structure
27

- The roof structure, or one or more sections of it, had no visible venting. This can result in high attic and roof surface temperatures, reduce the life of the roof covering materials, and/or increase cooling costs. High levels of moisture are also likely to accumulate in the roof structure or attic, and can be a conducive condition for wood-destroying organisms. Standard building practices require one free square foot of ventilation for every 150 square feet of attic space, and that vents be evenly distributed between the lowest points of the roof structure and the highest points to promote air circulation. Often this means that both soffit vents and ridge or gable end vents are installed. Recommend that a qualified contractor evaluate and install vents per standard building practices.
28
- One or more attic access hatches or doors were too small to allow easy access. Such hatches should be at least 22 x 30 inches in size, and in safely accessed areas. Recommend that a qualified person modify attic access points per standard building practices.
Electric
30


- Energized "knob and tube" wiring was found at one or more locations. This type of wiring was commonly installed prior to 1950. It is ungrounded and considered unsafe by today's standards. Over time, the wire's insulation can become brittle and fall apart or wear thin, resulting in exposed conductors and a risk of shock and/or fire. This wiring is also easily damaged by covering it with insulation (a common practice), and incorrectly tapping new wiring into it.
It is not within the scope of this inspection to determine what percentage of this property's wiring is of the knob-and-tube type, or to determine what percentage of the knob and tube wiring is energized versus abandoned. Recommend that a qualified electrician evaluate this wiring and make repairs or replace wiring as necessary.
Note that some insurance companies may be unwilling to offer homeowner's insurance for properties with knob and tube wiring. Consult with your insurance carrier regarding this. For more information, visit:
http://www.reporthost.com/?KNOBTUBE
31

- Wiring in the attic was routed on surfaces within 6 feet of one or more access hatches or doors, and was subject to damage. Wiring can be damaged when hatches are lifted and set aside, when stored items are moved into or out of the attic, etc. This is a potential shock and/or fire hazard. Recommend that a qualified electrician repair per standard building practices.
32

- One or more modern, 3-slot electric receptacles (outlets) were found with an open ground. Three-slot receptacles should have a hot, a neutral and a ground wire connected. Homeowners often install new 3-slot receptacles on older, 2-wire circuits that only have hot and neutral wires. This is a shock hazard when appliances that require a ground are used with these receptacles. Examples of such appliances include computers and related hardware, refrigerators, freezers, portable air conditioners, clothes washers, aquarium pumps, and electrically operated gardening tools. Where the electric system was installed prior to when grounded circuits were required (1960s), it is permissible to replace 3-slot receptacles with 2-slot receptacles to prevent appliances that require a ground from being plugged in to an ungrounded circuit. However, the client should be aware of this limitation when planning use for various rooms, such as an office. For newer electric systems, circuits should be repaired so grounded, 3-wire cables provide power to 3-slot receptacles. Recommend that a qualified electrician repair per standard building practices.
In addition the GFCI protected receptacles without a ground should be indicated that no ground is present (usually with a sticker).
33

- One or more electric receptacles (outlets) had reverse-polarity wiring, where the hot and neutral wires were reversed. This is a shock hazard. Recommend that a qualified electrician repair as necessary. For more information, visit:
http://www.reporthost.com/?RPRBasement
34

- No smoke alarms were visible. This is a potential safety hazard. A qualified electrician should install smoke alarms per standard building practices (e.g. in hallways leading to bedrooms, in each bedroom, on each floor and in attached garages). For more information, visit:
http://www.reporthost.com/?SMKALRM
35

- The outlet behind the stove in the main unit was loose and did not appear to be supported to the floor. This can cause damage to the wire. I recommend repair by an electrician.
36

- No carbon monoxide alarms were visible. This is a potential safety hazard. Some states and/or municipalities require CO alarms to be installed for new construction and/or for homes being sold. Recommend installing approved CO alarms outside of each separate sleeping area in the immediate vicinity of the bedrooms on each level and in accordance with the manufacturer's recommendations. For more information, visit:
http://www.reporthost.com/?COALRM
37

- One or more cover plates for switches, receptacles (outlets) or junction boxes were missing or broken. These plates are intended to contain fire and prevent electric shock from occurring due to exposed wires. Recommend that a qualified person install cover plates where necessary.
38

- Few receptacles (outlets) were installed in one or more areas by modern standards. This can result in "octopus" wiring with extension cords, which is a fire hazard. Consult with a qualified electrician about upgrading circuits with additional receptacles per standard building practices.
39
- One or more globes or covers for light fixtures were missing or damaged. Recommend replacing as necessary to avoid exposed bulbs. With closet lighting or where flammable stored objects are near light fixtures, missing or broken covers can be a fire hazard.
40
- One or more light fixtures were loose. Recommend that a qualified electrician repair or replace light fixtures as necessary.
The light did not appear to be getting power when the switch was used. Repair needed.
Plumbing / Fuel Systems
42

- The main water service pipe material was made of galvanized steel. Based on the age of the building, the apparent age of the pipe and/or the low-flow condition of the water supply system, this service pipe may have significant corrosion or rust on the inside and need replacing. Replacing the service pipe can significantly increase flow to the water supply pipes. Recommend consulting with a qualified plumber about replacing the main service pipe. Note that this can be an expensive repair since excavation is typically required.
43

- Significant corrosion was found in some water supply pipes or fittings. Leaks can occur as a result. Recommend that a qualified plumber evaluate and replace components as necessary.
44

- Low flow was found at one or more sinks, bathtubs and/or showers when multiple fixtures were operated at the same time. Water supply pipes may be clogged or corroded, filters may be clogged or need new cartridges, or fixtures may be clogged. Recommend that a qualified plumber evaluate and repair as necessary.
45

- One or more drain pipes or fittings were substandard. Recommend that a qualified plumber evaluate and repair as necessary and per standard building practices.
46

- The inspector heard gurgling sounds when plumbing fixtures (e.g. faucets, tubs, showers) were operated. Venting may be substandard or missing. Adequate venting is required to allow waste materials and water to drain freely, and to allow sewer gases to escape from the system. Recommend that a qualified plumber evaluate and repair if necessary.
Main kitchen.
47
- The main water shut-off valve handle was missing or damaged. It is especially important to be able to reliably operate the main water shut-off valve in an emergency, such as when a supply pipe bursts. Recommend that a qualified plumber repair as necessary.
48
- No expansion tank was installed for the water supply system. Expansion tanks are recommended when a property is on a public water supply system and the property's water system is "closed" via a pressure reducing valve (PRV), check valve, or backflow preventer. No room for expansion of water exists in this type of system. Thermal expansion occurs when water is heated during non-use periods. In a closed system with no provision for expansion, its effects can include:
- Backflow into the water main
- Damage to water heater connections, gas water heater flue tubes and pumps serving washers and dishwashers
- Leaking faucets
- "Weeping" of water through the water heater temperature-pressure relief (TPR) valve
- Noisy water hammer in the pipes
Expansion tanks can eliminate these problems by giving water a place to go when thermal expansion occurs. When a water heating cycle ends, or when any fixture is opened within the system, the impact of thermal expansion is reduced, and water drains out of the expansion tank back into the system. Recommend that a qualified plumber install an expansion tank per standard building practices.
49
- No sediment trap was installed in the gas supply line at the furnace and/or water heater. Sediment traps prevent damage to gas-fired appliances by trapping oil, scale, water condensation and/or debris. Recommend that a qualified contractor install a sediment trap per standard building practices.
50
- One or more leaks were found in water supply valves. A qualified plumber should repair as necessary.
51

- Based on visible equipment or information provided to the inspector, this property appeared to have a yard irrigation (sprinkler) system. These are specialty systems and are excluded from this inspection. Comments in this report related to this system are made as a courtesy only and are not meant to be a substitute for a full evaluation by a qualified specialist. When this system is operated, recommend verifying that water is not directed at building exteriors, or directed so water accumulates around building foundations. Sprinkler heads may need to be adjusted, replaced or disabled. Consider having a qualified plumber verify that a backflow prevention device is installed per standard building practices to prevent cross-contamination of potable water. Recommend that a qualified specialist evaluate the irrigation system for other defects (e.g. leaks, damaged or malfunctioning sprinkler heads) and repair if necessary.
Water Heater
55

- The water heater did not have earthquake straps or struts installed. This is a potential safety hazard in the event of an earthquake due to the risk of the water heater tipping over, gas lines breaking if it's gas-fired, or electric wiring being damaged if powered by electricity. Leaks can also occur in water-supply pipes. Recommend that a qualified person install earthquake straps or struts as necessary and per standard building practices.
Each water heater should have 2 straps.
56

- The temperature-pressure relief valve drain line was too short. This is a potential safety hazard due to the risk of scalding if someone is standing next to the water heater when the valve opens. Recommend that a qualified plumber repair per standard building practices. For example, by extending the drain line to within 6 inches of the floor, or routing it to drain outside. For more information, visit:
http://www.reporthost.com/?TPRVALVE
57

- The outer flame shield for the water heater combustion chamber was missing. This is a potential fire hazard. Recommend that a qualified person replace any missing flame shields.
58
- The hot water temperature was greater than 120 degrees Fahrenheit. This is a safety hazard due to the risk of scalding. The thermostat should be adjusted so the water temperature doesn't exceed 120 degrees. If the water heater is powered by electricity, a qualified person should perform the adjustment, since covers that expose energized equipment normally need to be removed. For more information on scalding dangers, visit:
http://www.reporthost.com/?SCALD
59
- PEX within 18" of the water heater should be removed and replaced with a solid pipe such as copper to prevent leaks. All work should be done by a qualified plumber.
Heating, Ventilation and Air Condition (HVAC)
62

- This heating system was a "gravity" type system, where air circulates without electric fans. They are inefficient, often heat unevenly, and can be dangerously hot. Recommend replacing this system for better energy efficiency.
https://www.nachi.org/gravity-furnace-inspection.htm
63

- One or more "livable" rooms had no visible source of heat. Examples of livable rooms include bedrooms, kitchens and living/dining rooms, NOT hallways, closets or bathrooms. Livable rooms without heat (e.g. heat register, radiator, baseboard or wall heater) can be uncomfortable and have high levels of moisture. Depending on the client's needs, recommend consulting with a qualified heating contractor to determine options for modifying or improving the heating system per standard building practices.
64
- Both evaporative coolers were winterized and were not tested. I was unable to determine the age and they may be old. I recommend that a qualified person evaluate and service them before use.
In addition I found that the covers above the evap coolers were not very efficient and were letting in cold air.
65
- I recommend that the heating ducts be professionally cleaned.
Note that if the gravity furnace is replaced that the ducts may need to be replaced because gravity furnaces use over sized ducts.
Fireplaces, Stoves, Chimneys and Flues
67

- One or more sections of B-vent or L-vent metal flue pipe were too close to combustible materials and/or insulation. This type of vent requires a minimum of 1 inch clearance to such materials. This is a fire hazard. Recommend that a qualified person repair as necessary. For example, by moving insulation, moving the flue pipe, installing a shield or making modifications to surrounding structures.
Kitchen
68

- The range could tip forward. An anti-tip bracket may not be installed. This is a potential safety hazard since the range can tip forward when weight is applied to the open door, such as when a small child climbs on it or if heavy objects are dropped on it. Anti-tip brackets have been sold with all free-standing ranges since 1985. Recommend installing an anti-tip bracket to eliminate this safety hazard. For more information, visit:
http://www.reporthost.com/?ATB
69

- Stove would not light and is in need of repair. I was able to confirm that the burners were getting gas and would light manually with a lighter.
The low setting was positioned next to the off setting. Many new stoves have the high setting next to the off setting to prevent leaving the stove on "low" and allowing gas to escape. I recommend replacement of the stove to one with the added safety benefits.
The electric stove was not fully tested due to the burners being unplugged.
70
- The kitchen sink drain pipe used an S-trap rather than a P-trap, or no P-trap was visible. Siphons and sudden flows of water in S-Traps can drain all the water out of the trap, leaving it dry. Sewer gases can then enter living areas. Recommend that a qualified plumber repair per standard building practices.
No vent was visible. Drain was gasping for air.
71
- No exhaust hood was installed over the cook top or range, and no wall-mounted exhaust fan was found nearby. This can be a nuisance for odor and grease accumulation. Where a gas-fired range or cook top is installed, carbon monoxide and excessive levels of moisture can accumulate in living spaces. Lighting may also be inadequate. Recommend that a qualified contractor install a vented and lighted range hood, with the exhaust fan ducted outdoors.
72
- One or more cabinets were loose, or were secured with too few or substandard fasteners. An adequate number of appropriate fasteners should be used. For wall-hung cabinets, inadequate fasteners can pose a safety hazard if cabinets fall. Recommend that a qualified person repair as necessary.
Drywall screws used to fasten cabinets.
73
- One or more sink drains were leaking. A qualified plumber should repair as necessary.
Bathrooms, Laundry and Sinks
75

- The toilet at location(s) #A was loose where it attached to the floor. Leaks can occur. Flooring, the sub-floor or areas below may get damaged. Sewer gases can enter living spaces. Recommend that a qualified contractor remove the toilet(s) for further evaluation and repair if necessary. A new wax ring should be installed and toilet(s) should be securely anchored to the floor to prevent movement and leaking.
76
- The bathroom with a shower or bathtub at location(s) #A and B didn't have an exhaust fan installed. Moisture can accumulate and result in mold, bacteria or fungal growth. Even if the bathroom has a window that opens, it may not provide adequate ventilation, especially during cold weather when windows are closed or when wind blows air into the bathroom. Recommend that a qualified contractor install exhaust fans per standard building practices where missing in bathrooms with showers or bathtubs.
Organic growth found on ceilings as a result of the excess humidity.
77
- One or more sink stoppers were missing or not functional at the time of the inspection. Recommend repair or replacement by a qualified person.
78
- One of the tub diverters were damaged and would direct all water to the shower head. The shower head was missing. Water is escaping from a tub and causing damage to the drywall. I recommend a splash guard in this area. Lastly drywall was left exposed in both showers and will allow water to more easily enter the wall cavity and allow mold growth. Repair needed by a qualified contractor.
79
- Water was leaking at the sink faucet base or handles at location(s) #A. Recommend that a qualified plumber repair as necessary.
Missing aerator as well.
80
- The toilet fill valve or float mechanism in the toilet at location(s) #B did not operate properly or was inoperable. Recommend that a qualified person repair as necessary.
In addition the tank cover was cracked.
81
- Gaps, no caulk, or substandard caulking were found between the bathtub and the walls at location(s) #A and B. Water may penetrate these areas and cause damage. Recommend that a qualified person re-caulk or install caulking as necessary.
82
- The bathtub drain stopper mechanism at location(s) #A was missing. Recommend that a qualified person repair or replace as necessary.
83
- Uneven flooring was found in the bathroom. It is possible that the wood beneath is rotted based on the unlevel flooring and proximity to the tub. Any rotted wood should be replaced.
84
- The bathtub at location(s) #B drained slowly. Recommend clearing drain and/or that a qualified plumber repair if necessary.
Interior, Doors and Windows
87

- Handrails at one or more flights of stairs were missing. This is a potential fall hazard. Handrails should be installed at stairs with three or more risers or where stairs are greater than 30 inches high. Recommend that a qualified contractor install handrails where missing and per standard building practices.
In addition the stair treads were damaged and pose a fall hazard.
88

- One or more stair risers were damaged and in need of repair or replacement.
89

- Condensation or staining was visible between multi-pane glass in one or more windows. This usually indicates that the seal between the panes of glass has failed or that the desiccant material that absorbs moisture is saturated. As a result, the view through the window may be obscured, the window's R-value will be reduced, and accumulated condensation may leak into the wall structure below. Recommend that a qualified contractor evaluate and repair windows as necessary. Usually, this means replacing the glass in window frames.
Be aware that evidence of failed seals or desiccant may be more or less visible depending on the temperature, humidity, sunlight, etc. Windows or glass-paneled doors other than those that the inspector identified may also have failed seals and need glass replaced. It is beyond the scope of this inspection to identify every window with failed seals or desiccant.
90

- Floors in one or more areas were not level. This can be caused by foundation settlement or movement of the foundation, posts and/or beams. Significant repairs may be needed to make floors level. Recommend that a qualified contractor and/or engineer evaluate further. Repairs should be performed by a qualified contractor.
91
- Some exterior door hardware, including deadbolts were inoperable. Recommend that a qualified person repair or replace as necessary.
Unit B
92
- One or more interior doors were damaged. Recommend that a qualified person replace or repair doors as necessary.
Bathroom, Unit A
93
- One or more walls were damaged and/or had substandard repairs. Recommend that a qualified person repair as necessary.
94
- One or more interior doors were sticking in the door jamb and were difficult to operate. Recommend that a qualified person repair as necessary. For example, by trimming doors.
95
- Lock mechanisms on one or more windows were damaged. This can pose a security risk. Recommend that a qualified person repair as necessary.